Fire Safety Requirements for Chemical Storage Areas in Vapi
April 22, 2025
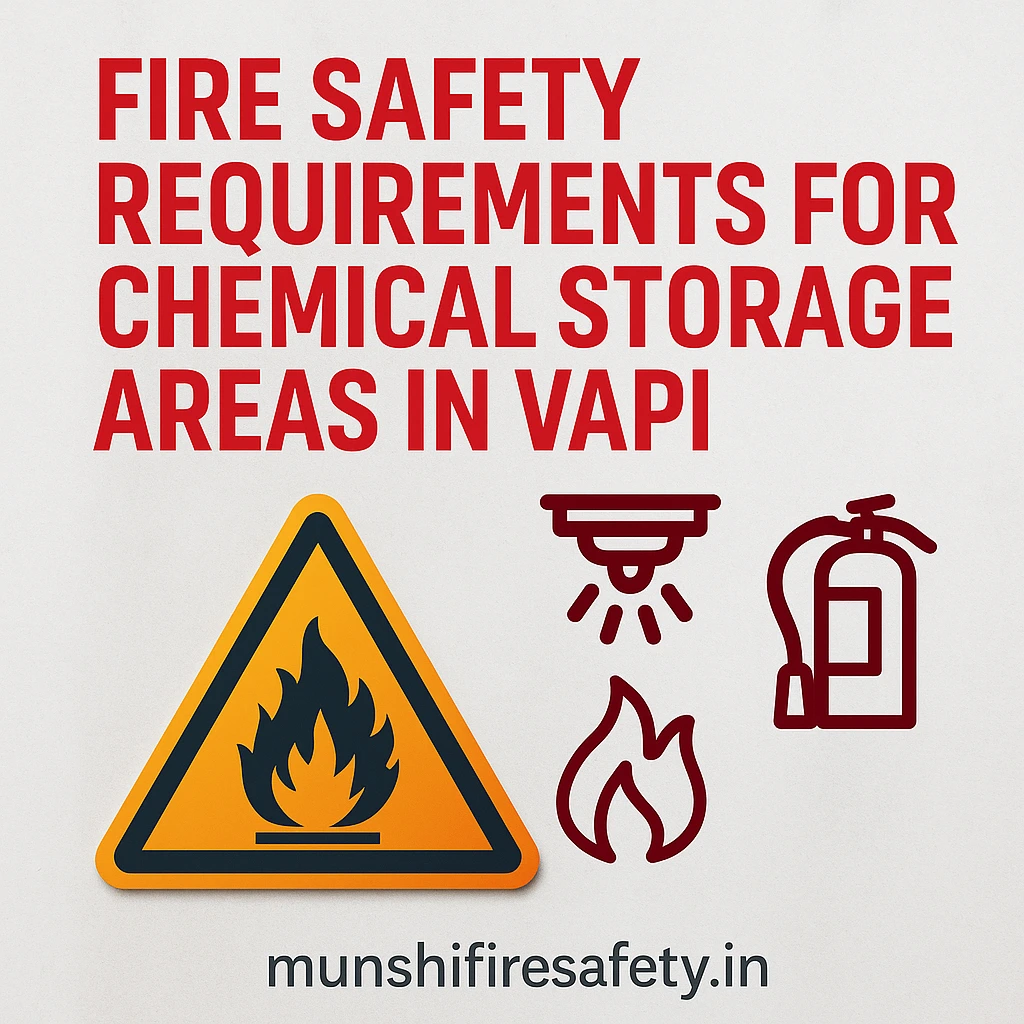
Table of Contents
Ensure compliance and safety in Vapi’s chemical warehouses with guidelines on facility design, fire‑protection systems, emergency planning, and regular maintenance tailored to GIDC and local regulations.
Introduction
Chemical storage areas present unique fire hazards—volatile compounds, reactive mixtures, and large volumes of flammable liquids. In Vapi’s GIDC estates, where chemical plants cluster, adhering to strict fire‑safety requirements is not only regulatory but essential for protecting workers, assets, and the environment. This guide outlines the key measures you must implement.
1. Regulatory Framework and Standards
- Gujarat Fire Prevention and Life Safety Measures Act, 2013: Mandates automatic detection, suppression systems, and trained personnel in chemical zones.
- National Building Code (NBC) Part 4: Specifies safe storage distances, construction materials, and fire‑resistance ratings.
- NFPA Standards (10, 30, 13): Provide best practices for portable extinguishers, flammable liquid storage, and sprinkler systems.
Interconnected Insight: Aligning local statutes with international norms ensures both legal compliance and global best practices.
2. Hazard Identification & Classification
- Flammable Liquids (Class I & II): Petrol, solvents—high flash points below 60 °C.
- Combustible Liquids (Class III): Oils, greases—flash points above 60 °C.
- Reactive Chemicals: Peroxides, nitrates—may self‑heat or detonate.
Action Step: Maintain an up‑to‑date inventory and Safety Data Sheets (SDS) for all stored materials.
3. Facility Layout & Construction
Minimum Separation Distances:
- 5 m between tanks or 1.5 × container height
- 9 m to property boundary in GIDC zones
Bunding and Drainage: Concrete containment bunds sized to 110% of largest tank volume; sloped floors directing spills to collection pits.
Fire‑Resistant Walls: EI 120-rated partitions between storage bays.
4. Detection & Alarm
Smoke and Flame Sensors: Deploy in enclosed pump houses and open‑air tank fields respectively.
Heat Detectors: Rate‑of‑rise type above chemical pallets.
Alarm Panels: Must connect to on‑site control room and Vapi Fire Brigade alarm line.
5. Inspection, Testing & Maintenance
- Daily Checks: Visual inspection of extinguishers, hydrant valves, and clear access routes.
- Monthly Tests: Alarm functionality and sprinkler flow‑tests.
- Annual Servicing: Full system certification by an ISI‑approved vendor.
Holistic Note: A maintenance log sustains system integrity and satisfies Gujarat Fire Department audits.
6. Training & Emergency Response
Staff Drills: Quarterly fire‑drills tailored to chemical‑spill scenarios.
First‑Responder Teams: Equip 5 % of workforce with FAT (Fire‑Alarm & Attack Team) training.
Evacuation Routes: Clearly marked in Gujarati and English, leading to assembly points at least 30 m from storage.
Conclusion & Next Steps
Implementing these measures transforms your chemical storage area from a potential hazard into a resilient facility. By integrating robust design, detection, suppression, and human‑response elements, you create a safety network that protects lives, property, and business continuity.
📞 Contact Munshi Fire Safety for a comprehensive fire‑safety audit in Vapi: tailored designs, certified installations, and AMC packages for chemical warehouses.
Admin
Fire Safety Expert
Stay Updated
Get the latest fire safety tips and news delivered to your inbox.